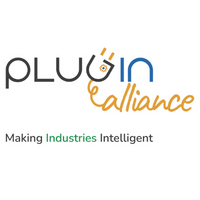
Plugin Alliance
View Brand PublisherCommunity Voices: How Jidoka’s AI-powered solution helped biscuit manufacturers eliminate defective biscuits
While Jidoka has been improving efficiency across multiple sectors with their award-winning Automated Cognitive Quality Control Solution, one of their distinct impacts can be seen through their work with a renowned biscuit manufacturer.
Founded by Sekar Udayamurthy, Dr Krishna Iyengar and Vinodh Venkatesan, Jidoka combines artificial intelligence with automation to deliver cognitive inspection of defects in the manufacturing domain.
Coming from the manufacturing space, the founders had noticed that the visual inspection done by companies was predominantly a manual process. Traditional machine vision had failed and no product in the market provided a solution out of the box. “There was no solution that actually solves the customer problem entirely, so we decided to build it ourselves,” said Sekar.
The growth story
Manufacturing was heavily reliant on individuals, which could lead to inconsistency. There was a conflict between speed of production and quality control. Alongside this, existing machine vision solutions were not equipped to handle drift in the manufacturing process.
To that end, Jidoka leverages AI to deliver value across three main sections such as better quality, savings and cost optimisation, and automating tasks. This helps in enhancing the quality and efficiency of manufacturers. Their use of smart technology helps customers in going beyond traditional machine vision and achieve accuracy rate up to 99.5 percent.
“Jidoka has found the PMF and is currently scaling in India. Jidoka has grown 5X in the last year and is looking to continue this growth in India,” revealed Sekar.
The company has worked with customers across sectors like pharma, automotive, food, general manufacturing, and warehouse and logistics. Some of their marquee customers include Marico, Mondelez International, Nexteer, ZF Rane, Faurecia, among others.
The Jidoka edge
While Jidoka has been improving efficiency across multiple sectors with their award-winning Automated Cognitive Quality Control Solution, one of their distinct impacts can be seen through their work with a renowned biscuit manufacturer. The team helped the manufacturer eliminate defective biscuits before packaging.
A leading ‘sandwich biscuit’ manufacturer wanted a solution to automatically identify and reject faulty biscuits in the manufacturing process.
Biscuits are manufactured at a speed of 4,500 parts per minute. The inspection would happen manually with people trying to inspect on the production line at such high speeds. The faulty biscuit production rate is about 1.5 percent of total biscuits manufactured. Of this, about 50 percent could be identified by people at such high speed. The manual inspection would result in worker fatigue in a high pressure work environment, while also allowing 0.75 percent of faulty biscuits per day (about 50,000 nos.) to be shipped to the market. There would also be no record or data on the type of defects that were occurring for analysis.
Defects on the biscuits included reverse orientation of biscuits in the sandwich (top and bottom biscuit), cream overflowing from the sides, cracks and damages in the biscuits.
While working with the biscuit company, Jidoka leveraged their AI software Kompass, which identifies defects at rates of over 99 percent sensitivity with very minimal false positives. Jidoka placed six cameras across two locations in the manufacturing line to monitor the biscuits. The industrial cameras sent the images of every individual biscuit before and after the cream placement in the biscuits to a central server. Their software Kompass used AI to identify the critical defects along with processing the decision as per the business logic defined by the manufacturer.
The result was communicated to the ejection mechanism hardware which removes faulty biscuits from proceeding to the next stage – which is packaging. The camera image grabbing, AI software decision and the ejection worked in sync at speeds of 4,500 biscuits per minute.
The integration with customer machinery ensured there is no change in the process or layout to the manufacturer while also achieving automated inspection and rejection of bad biscuits.
Due to Jidoka’s digital transformation, faulty biscuits shipped to the market reduced by 98 percent. There was no manual inspection needed, saving INR 1 million+ per year. Alongside this, there is increased consumer perception in the quality of biscuits.
The way ahead
“We have heavily invested in scaling our products in India and to grow in North America and Europe. We are looking to roll out Version 3.0 of the Jidoka Visual Inspection platform,” said Sekar.
About Community Voices
Community Voices is a series of articles from the Innovent 4.0, an exclusive industry technology conclave from the Plugin Alliance — a first-of-its-kind Industry 4.0 alliance in India — with the aim to showcase India’s role in the Fourth Industrial Revolution. In tune with the event, the series will continue to highlight stories from Industry 4.0 startups.
that spotlights solutions and startups helping India’s manufacturing and supply chain industries benefit from smart technology. The series leads in to