TCS says digital is the future, partners with Rolls Royce for industrial-digital IOT
Neil Crockett, Chief Digital Officer of Rolls Royce, says this partnership enables the manufacturer to use the TCS platform for real-time analysis of all their engines.
In a move that is significant to the IT services industry, TCS announced that it will partner with Rolls Royce, the $16-billion-in-revenues manufacturing giant, to usher in an era of artificial intelligence and machine learning. This will be a major move in the IT services industry as IOT is a $3-trillion opportunity globally. TCS along with Rolls Royce will simulate “digital twins” to reduce the time to market between R&D and the commercialisation phase.
A digital twin is a process wherein a digital image of the component is created on a real-time basis. Based on large sets of data, Rolls Royce can tell regulators about the efficacy of the component and its safety specifications. “This reduces the time to market and brings down the cost,” says Ben Story, Strategic Marketing Director at Rolls Royce. The company along with TCS will also work with startups and other companies to figure out machine learning and artificial intelligence synergies in making real-time data for end users of Rolls Royce engines.
Ben adds that in the digital twin module, they can have product, production, and performance twins. “We are using data to tell them regulators about the safety s of a part without really having to manufacture anything,” says Ben Story.
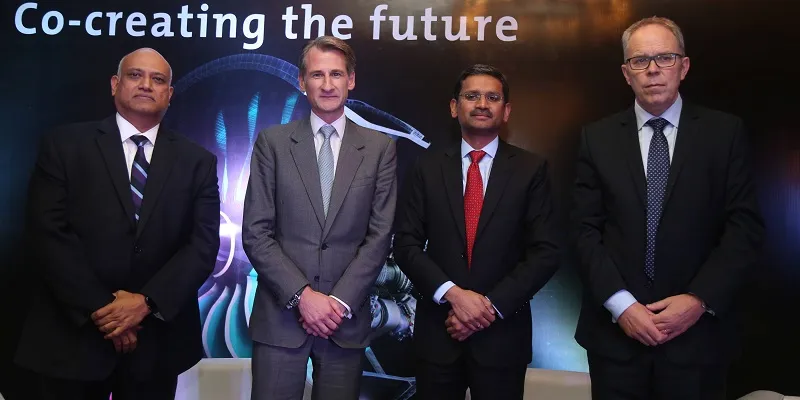
The “production twin” is about automating production environments digitally and creating a flow for the production process. In a “performance twin” module, the product’s lifecycle is automated to understand its rate of failure. These things are only possible by taking in years of data about flying and combining maintenance manuals of engines.
“This data also allows us to design and make engines better,” says Ben.
The TCS Connected Universe platform, which already has many airline companies, allows Rolls Royce to receive live stream data from the several IOT devices in the aircraft, and prescribe diagnostic services. Rolls Royce hopes to use the TCS platform on other engines such as ship and train engines in the long run.
“We signed up TCS because the platform is scalable, open, and secure,” says Neil Crockett, Chief Digital Office of Rolls-Royce. The world is moving towards using data and getting insights and every company in the manufacturing industry is preparing for this.
“We believe the world is about collect, share, and analyse,” says Neil. He adds that IoT data is of utmost value to customers. “We will work in areas like artificial intelligence and machine learning over the months and years.”
Why is this significant for TCS?
Today, only 10 percent of the revenues of the top IT companies come from platform-based services.
“Rolls Royce is a gold standard of innovation and it is great to work with them. The platforms for Industry 4.0 was born out of CTO labs where the platforms are collaborative and use data from several sources,” says Rajesh Gopinath, Managing Director of TCS. He says IOT offers a ton of functionalities to develop, deploy and launch products and services quickly. The future is in agile IT and cloud based services.
Companies like Infosys have the Edgeverve platform that offers similar services for banking, retail and manufacturing companies. This is a fundamental shift in the IT services business where the money will be driven by outcomes and the contract time frames will be shorter.
TCS says that the deal value – with Rolls Royce – is very big and the company is one among the top three TCS’ clients in their manufacturing segment. However, TCS will surely not be the first to be announcing such a big partnership.
According to a NASSCOM and Deloitte report titled Revolution in the Making, India will have 1.9 billion IoT devices installed, from the current base of 60 million devices, with a market size of $9 billion. If this ‘really’ happens, India’s installed base will be 10 percent of the total volume of the globe. In terms of market size, India will be 0.40 percent of the total global value of $3 trillion.
To seal this further, it is industrial adoption that is really driving this wave. There are 5,000 farmers in Maharashtra and Gujarat who are using M&M tractors and they will tell you how the internet is benefiting them. Each of their tractors generates data worth 5MB per day; only a select few parameters are programmed to be captured, otherwise, a vehicle can generate volumes of data. Their vehicles are fitted with Bosch’s IoT devices whose sensors can track the farmers’ vehicle operations on a real-time basis.
Soumitra Bhattacharya, MD of Bosch Limited, says: “On a real-time basis, M&M can tell when their tractors are going to fail and therefore help the farmer from preventing the event by fixing the problem.”
In the factories of packaging giant Manjushree Technopack, employees are working with Entrib Analytics Technologies — a startup whose product ShopWorx is connecting the entire shop floor. It comprises of more than 100 machines to plan the movement of materials and coordinate with production. In Manjushree’s factories, it does not stop just there; they use machines called Husky, manufactured by Husky Injection Molding Systems in Germany, which can track the failure rate in machines in real time.
Vimal Kedia, Managing Director of Manjushree Technopack, feels information is “the key while using hundreds of machines on the shop floor and we need to visualise usage to stay on top of the game”.
While these are Indian examples, General Electric too is making inroads in IoT globally.
Its work in renewable energy is well documented, especially where the company had to determine the speed of the wind and the weather. GE’s technology team demonstrated that their self-learning algorithms, when applied to real wind farms, produced results that were five to seven percent better than the best solution available in the market. They garnered a better prediction rate with 94-95 percent accuracy. GE’s work was cited by the Government of India, and this solution is now deployed at five different sites in the country.
General Electric has already been using data from all its machines since 2010 to understand their rates of failure so as to predict failure before it occurs. It has invested in machine learning algorithms to figure out the rate of failure on its jet engines, on wind turbines, and healthcare equipment.
Vinay Jammu, Technology Leader, Physical-Digital Analytics at GE Global Research, says: “We are using the digital twin model to understand the relationship between virtual and physical aspects that affect a machine. We did this with our wind turbines in South India.”
GE combines wind turbine data with weather data and the data generated to capture wind movements, to predict the impact on a machine.
Vinay adds that statistical models must be able to predict the rate of failure and suggest prescriptive services dynamically. GE calls it the “digital twin model”, where an IoT device is simulated by combining data and running it through algorithms. The learning from this determines the delivery of the physical asset onto the field.
So, for Rolls-Royce, India is a big bet — with its engineering centre housing 1,300 engineers who will closely work with data