How 27-year-old Akash Gupta built the largest automation startup of India
For Akash Gupta, a journey which started with building humanoids has shaped into one of the largest automation companies of the world today. Our candidate for this week’s Techie Tuesdays, Akash is the Co-founder and CTO of GreyOrange, an automation startup that provides warehousing solutions.
What does it take to be the CTO of one of the largest hardware and automation startups in India and the world at the age of 27? The secret, according to Akash Gupta, the Co-founder and CTO of GreyOrange, lies in having strong fundamentals, the ability to quickly learn and unlearn new technologies and learning from the mistakes/failures even more quickly.
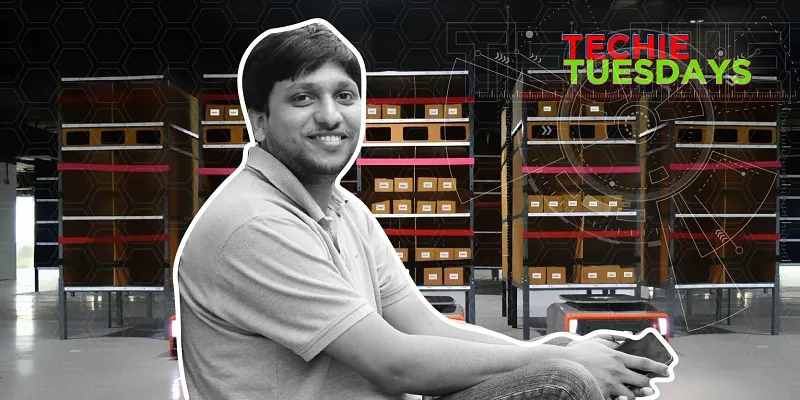
A BITS Pilani graduate in Mechanical Engineering, Akash’s interest in building robots (humanoids) was strong that he built one in his college days. Unlike most students who tend to get emotionally attached to college life, our Techie Tuesdays candidate of the week, Akash, was was happy to finish his degree in three years and be out of the college.
YourStory caught up with Akash recently at his Gurgaon office to retrace his journey.
The geeky athlete from Kanpur, Uttar Pradesh
Akash was born in Auraiya district of Uttar Pradesh, situated 400 km from Delhi. His father worked in railways and was posted at Dibiyapur railway station. He studied there till class IV. When his family moved to Kanpur he joined the Puranchandra Vaidyaniketan school there.
Akash started coding in class VI with GW-BASIC and learnt C the next year from his sister’s book Let Us C. Subsequently, he developed an interest in 3D animation and learnt 3ds Max and Maya. This kept him busy in class IX and X. Akash believes that his interest in 3D animation plateaued partly because of limited exposure to algorithm at the time.
Incidentally, this geeky student was the 100m champion in school. However, the IIT JEE preparation in class XI and XII weaned him away from track and field activities forever.
Akash joined the Mechanical Engineering department at BITS Pilani in 2008. One of the predominant thoughts in his mind then was that he had solved enough problems on paper, and now wanted to do things in real life. He says,
I could draw a DC or an AC motor on paper very well, but looking at the motor of the ceiling fan, I couldn't tell which one of those it was.
Related read - Meet Kiran Bhat—the man who engineered Hulk and Tarkin to win 2017 sci-tech Oscar
Introduction to robotics and AcYut
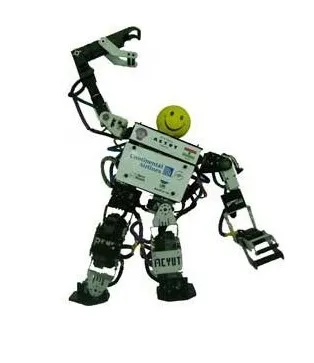
In his first year, Akash saw a demo of the AcYut humanoid project. To join the team, he gave the AcYut test where he was asked to make a 3D emblem of BITS Pilani on Inventor software. Being good at 3D animation, Akash made the cut easily and started working with the team AcYut in his very first month in college. He wanted to learn as much as possible.At AcYut, Akash started by designing the mechanical parts and then manufacturing them.
As a team member, he had full access to the CNC (Computer Numerical Control) Lab for manufacturing. He learnt to write G Code (input for CNC machines) and to run CNC machines. In the first year, the team made three versions of the complete mechanical structure of AcYut. Akash says,
I was so much into it that I couldn't see anything else and fortunately BITS (Pilani) gives you that flexibility.
Testing waters at Robo Games
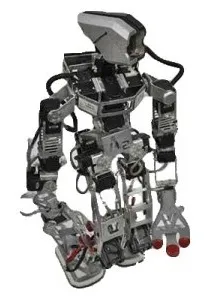
In October 2008, Akash went to Japan to participate in a robotic competition. This was his first exposure to an international technology-based competition which helped him understand the global benchmarks for such competitions. Team AcYut was then planning to participate in the Robo Games next year (2009) for which they started building two robots. Akash picked up micro-controller programming and took his understanding of robotics further.
In AcYut-II, the team used bust motors (motors serially connected to each other using RS-485). There were two series of 16 motors each and hence, writing fool-proof protocols was not easy for them. Akash says,
In humanoids, the most complicated thing is stability. We underestimate how easily we walk (and balance). Walking is very difficult to simulate. With a lot of enthusiasm, we chose six DOF (degree of freedom) leg and then we spent good two months solving the inverse kinematics for them.
Even after figuring out the right inverse kinematics model, it took the team another six months to put it in codes and ensure that those signals go to the motors at the right time and they behave as intended. Team AcYut used ATmega1280 for controlling the complete bot and 3mm sheets of 6061 aluminium to manufacture the brackets (chassis structure on which you mount motors etc) of AcYut.
Since the workshop occupied the day time, Akash (and team AcYut) got to work only at night.
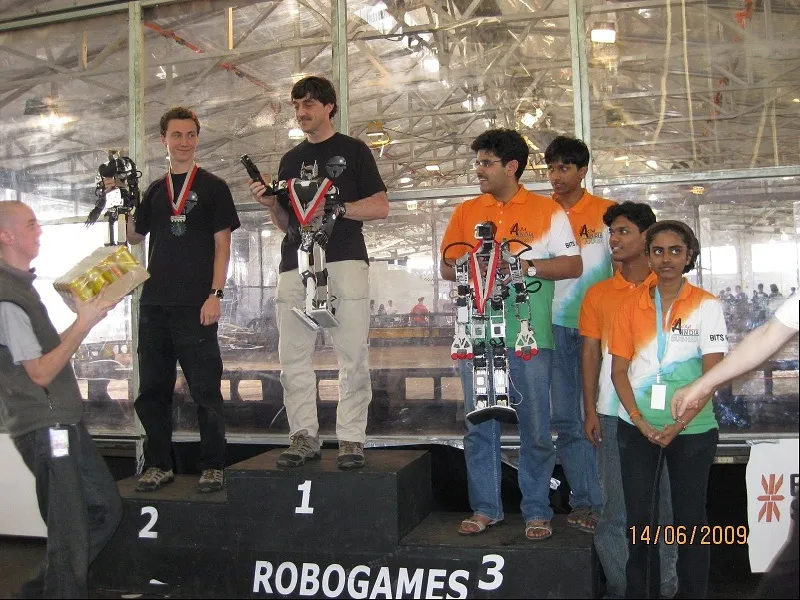
Eventually, the team won the bronze model at the Robo Games in San Francisco.. The main competition at the Robo Games was humanoid Kung-Fu where the robot which can knock down the other robot three times wins.
The internship and the haunted house project
At the end of his first year, Akash and Samay Kohli (Co-founder GreyOrange and team member AcYut) got an internship at University of Louisiana where they worked at the CajunBot Lab on an autonomous vehicle project for some time. At the university, they met Thomas Chance, CEO, C&C Technologies, which built equipment for underwater surveying. This was their first exposure to industrial robotics. The duo worked at C&C Technologies in the areas of mechanical design, electronics and microprocessors.
One of the major projects Akash worked on was the SONAR stabilising system which solved the problem of mapping the ocean bed accurately and get rid of the inconsistency caused by the waves. This included fair amounts of mechanics and electronics. Since Akash and Samay had time on their hands, they went on to build a kind of Disney ride (by joining two trailers) in a haunted house owned by Thomas. Akash says,
One could sit on a trolly and go through the rooms which were themed differently like earthquake room, laser room. More than 200 microcontrollers were working in sync with 5 computers and 1,000 air pistons (for doing a lot of actuations) to make it all happen. The entire setup cost almost $250,000.
In his second year, Akash spent a lot of time on electronics, designing and manufacturing PCBs end to end. The AcYut team won the gold and silver medal at the Robo Games. They built an exoskeleton suit wherein if a person wears this suit and moves his/her hands, then the robot will copy/replicate it. They went to the Ideen Expo in Germany with this project. Akash visited the BMW manufacturing plant there which helped him understand the importance of factors like reliability in the automation industry.
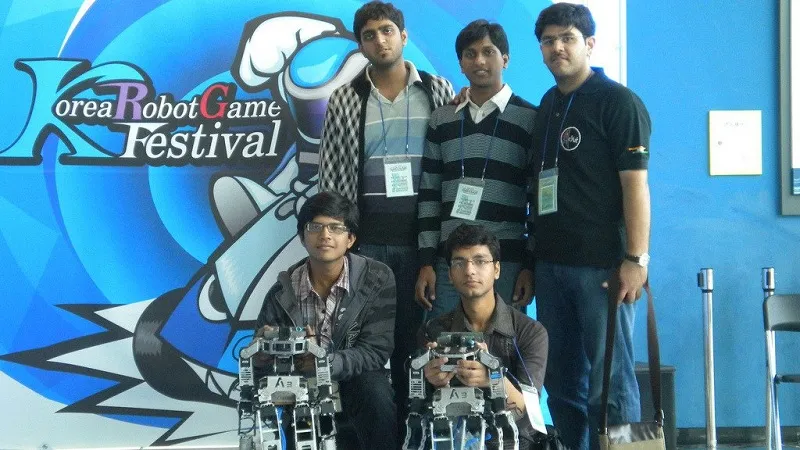
Akash recalls meeting Wolfgang Hoeltgen during the visit. He is one of the earliest angels and a strategic mentor to the founding team at GreyOrange.
Seeds of GreyOrange
In January 2011, Akash and Samay were invited to take part in a humanoid hand (robotics) workshop at IIT Bombay. Soon, other colleges too invited them and that’s when they started thinking about starting a company. Also, since the work had started, Akash was very keen to come out of college as soon as possible. At the time he was juggling between AcYut, GreyOrange and his studies (curriculum). He used to be in Delhi from Saturday to Monday (running GreyOrange) and back in Pilani from Tuesday to Friday (to attend the labs, as a part of the curriculum were on Tuesdays and Fridays).
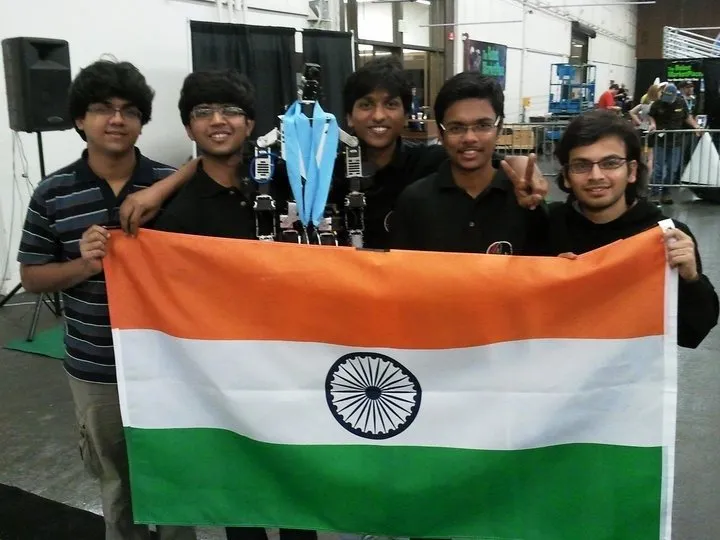
Akash and Samay started making kits for the workshops which gave them an experience of doing things at scale. By now, they were done with the Robo Games and started targeting the Robo Cup. While the Robo Games had remote controlled robots, the Robo Cup had completely autonomous (robot) 2*2 soccer.
While preparing, Akash got into image processing, cognitive understanding, vision systems and started solving the localisation problems. He understood the complexities of gyroscope, magnetometer, accelerometer.
Akash finished his college degree in three years somehow and took the final-year internship at GreyOrange. In June-July 2011, he shifted to Samay's house in Delhi marking the formal start of GreyOrange.
Also read - From UP to the US: The journey of Abhinav Asthana and his affair with APIs
From workshops to white labeled products
Even though Akash and Samay were making good money through workshops, they were clear that they were not going to do it for long. Soon, they started building white labeled products for other companies. These included:
- An image processing project for C&C Technologies.
- A portable medical device (with a suction pump which calculated (and regulated) the indicative pressure required) to suck the puss out of wounds and did the task.
This gave Akash an exposure to different standards of coding and manufacturing. He used Qt language (application development framework based on C++) for the software. He says,
I started understanding the importance of getting the right abstraction (very well structured in programmes) from the real world. For example, while programming for a pump, you've to make sure that all the different attributes of that pump are kept in your data structure in order to perform different actions on it. This becomes even more important when we're building longer-term products.
Setting the rules
After building 3-4 white label products, Akash realised that he (and Samay) were playing with way too many technologies and products. Hence, they decided to choose an industry and build products only for that. While researching to finalie the industry, they wrote down some rules to help them choose the right industry:
- It has to be a global problem.
- The solution to the problem has to be disruptive enough.
- It has to be a problem which requires both software and hardware application. This came from the thought that Akash and Samay wanted to build products with simple elegant hardware and super complex software.
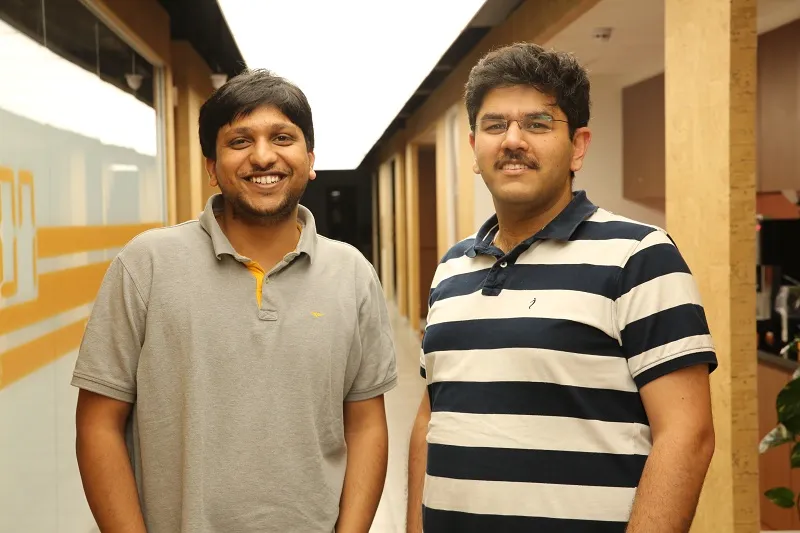
They finally zeroed in on three industries:
- Oil and gas -- robots for oil and gas industry maintenance.
- Products for railway inspection (to help replace the maintenance of thousands of kilometers of railway track).
- Supply chain and warehousing.
They chose option #1 and built a prototype. They proposed the idea of maintenance of tanks to a company. They even gave them the design. Unfortunately, the company floated the tender with their requirements sharing the design submitted by GreyOrange and somebody else bought the tender. Akash recalls, “Being a startup we were left with nothing. We even filed a complaint but couldn't give more time to it and had to let it go.”
They then moved to supply chain. Akash visited a lot of warehouses, enough to convince him that a lot needed to be done there. He started looking at goods to person systems and found that it could be made much more efficient using Grey Prange’s solution of using an elegant hardware and a complex software. The first thought was to build a bot.
You may also like - Meet Mitesh Agarwal—the ‘brain’ of BITS who’s heading technology at Oracle India
GreyOrange – taking the shape
According to Akash, building a butler system is almost like bringing four large products together to make a complete system. It will have bots, pick-put stations, MSUs (mobile storage units) and a software that runs robots and business logic of inventory management. Akash and Samay spent the first few days understanding the entire problem and figuring out what the solution will be like. Akash says,
Our thought process was slightly different than what Kiva Systems (now Amazon Robotics) was doing. Kiva had a lot of Swan robotics which refers to distributed intelligence. Only the main server didn't have the onus of being intelligent. Bots were intelligent as well. We wanted to have a simple hardware and table up all the complexity on the server side.
This gave Grey Orange a flexibility which is desirable in the warehouses. Keeping the product software centric helped it and the hardware acted as more of generic agents.
Akash and Samay knew that it's going to take them more than two years to build a butler system. And they also understood that survival of a startup for two years without revenues is very difficult. This thought coupled with an opportunity to build a sortation system for warehouses, made the duo explore it after visiting Flipkart's first ever warehouse. Akash says,
We decided to build a sortation system on the side while working on the butler system. It was a hard decision to take as we were a team of only ten people and bulter system itself was hard enough problem to solve. Technically it's not advisable to do such a thing.
For two years, the team kept switching between sortation system and butler systems as working in parallel wasn't possible.
Technology – Butler System and Sortation System
Lifting (500 kg weight) was one of the most challenging problems to be solved in order to build a butler system. The team at GreyOrange used a complex dual scissor lift mechanism to lift and built multiple prototypes. Akash says, “In the hardware world, it's better to build as many prototypes as possible and fail rather than getting stuck with building a perfect prototype.”
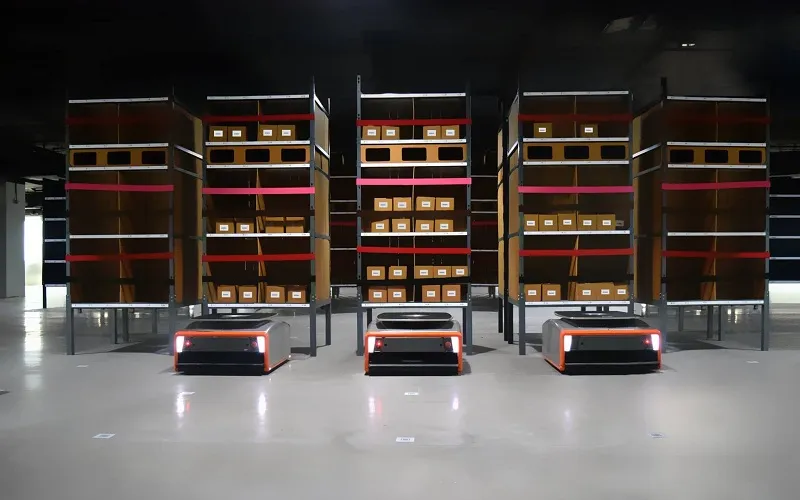
Akash drew the architecture of the robot (butler) with safety system, navigation system and communication system. On server side, the team chose Erlang as the language for the main system. It was a hard decision as there were very few programmers who knew the language. Akash says,
At that point we had a dream to run 1,000 robots in a single warehouse. We couldn't find any other language or stack which allowed so many agents running in a soft real-time system.
Initially, the team used Hub motors where the motor and suspension was on wheels but later on scrapped it as it created a lot of problems. After three revisions, they got the design and production of the gear box right. Akash adds, “Lack of prototyping ecosystem in India created further problems and delays. We resorted to doing things in-house as we couldn't be dependent on outside shops.”
Finally, in November, Grey Orange launched its first prototype. Now, the challenge was to make them manufacturable (so that robots aren't handcrafted). That took another 8-9 months. In the meanwhile, the team received an order for building sortation system. They decide to build a completely modular sortation system, so that even when one of the arms stops functioning, the rest can still work. An overall control system was designed for this. Akash says, “Because PLCs (programmable logic controllers) had a lot of limitations, we built our own control systems. The sortation system was relatively less complex on the server side and fairly complex on the embedded side.”
The first butler system was installed in Hong Kong. It had a small ten bot system, 200 MSUs, 2 pick-put stations, auto charging.
Related read - Meet the co-creator of Julia programming language, Viral Shah
The virgin problem of the sortation system
Usually, sortation systems are built to sort boxes. Akash too thought so and used IR (infra red) sensors. But when he received the sample packs from Flipkart, he realised they are poly packs (and not boxes). The IR sensors behaved very differently for these poly packs. Akash adds, “This was the first ever sorter built for e-commerce company in India. And outside India, everyone used a box. So, this problem was left virgin.”
Akash and his team fixed the problems of motor heating, slipping of belt, incorrect counting of the package, before installing the system at Flipkart warehouse. Moving the sorter from Gurgaon to Bangalore was very challenging. It was only now that the team started thinking about transporting the machine. It was a 40-45-ft-long machine which had to be dis-assembled and transported. It was a humongous task which taught that designing to make it work isn’t enough. One has to design while making sure that the system is assembled, dis-assembled, supported, moved comfortably.
Scaling tech
From the current capacity of supporting 1,500 to 2,000 butlers (bots), GreyOrange wants to build systems which can support infinite number of bots. The team has converted its monolithic architecture to micro services based architecture to achieve scale.
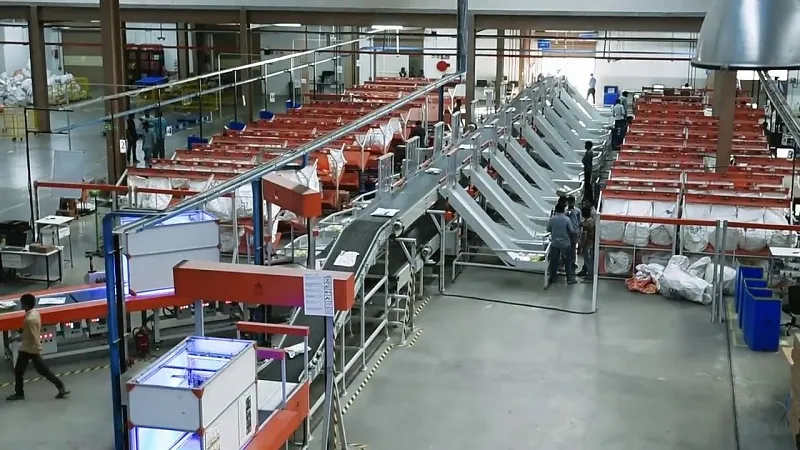
For GreyOrange, if servers go down, it's not just the website which will go down, but also hundreds of robots with 500 kg weight on each will crash with each other. Hence, Akash and his team has to be even more careful while writing algorithms and ensure that any path reserved by a bot isn't taken by anyone else and that the orders are optimised in the best possible ways. According to Akash, right choices of architecture, stacks, thinking it through, being flexible and ensuring that the team focuses in-depth into modules has helped the company.
Technical challenges and solutions
Some of the key challenges which Akash and his team are solving at GreyOrange are as follows:
- Hardware: In Japan, design is seen very differently as compared to the US, EU or SE Asia. In some geographies, people need more colours and info on screen whereas in others they prefer it minimal. Ensuring a universal international product (which appeals to all) in terms of design and user experience is a big challenge.
- Software: Different industries have different characteristics of warehouses. Inventory, order, operations characteristics and process flows of warehouses are largely different from each other. Building common software to support each of them is not easy as the system has to learn from the historical data. The operators adjust their behaviours in the pick-put stations accordingly and the algorithms are extremely receptive with data and characteristics.
- Support: Any product sold at this point of time (being an industrial product) needs to be supported for the next ten years. In doing so, supply chain becomes very important. It has to be ensured that spare parts and support systems are in place for the next ten years. GreyOrange uses component engineering to solve this. Akash says, “It may look like a non-engineering problem but it isn't the case in reality.”
- Availability of hardware components for quick prototyping stills remains a big challenge for the company. Akash says, “We've been exploring the China ecosystem aggressively to get supply chain guys to help us accelerate our design prototyping process for complex parts.”
In the last few months, rapid expansion to multiple geographies has brought in some operational problems like translating documentation, communication, screens, APIs, databases in five languages. To solve this, the team has built a clear framework and web interface for translators who get notifications sprint by sprint of new strings that are coming.
Akash believes that the hardware ecosystem in India has definitely evolved in this decade but the change is minimal. He says, “People have become more supportive of working for prototypes of startups because somewhere they have seen startups becoming big."
Four years ago, when Akash went to a company which produced suspensions for automobiles, he was turned down immediately because of the low production volume requirement (relative to what the company produced for automobiles) and a lack of understanding of startups. But a year ago, when he spoke to them again, they agreed.
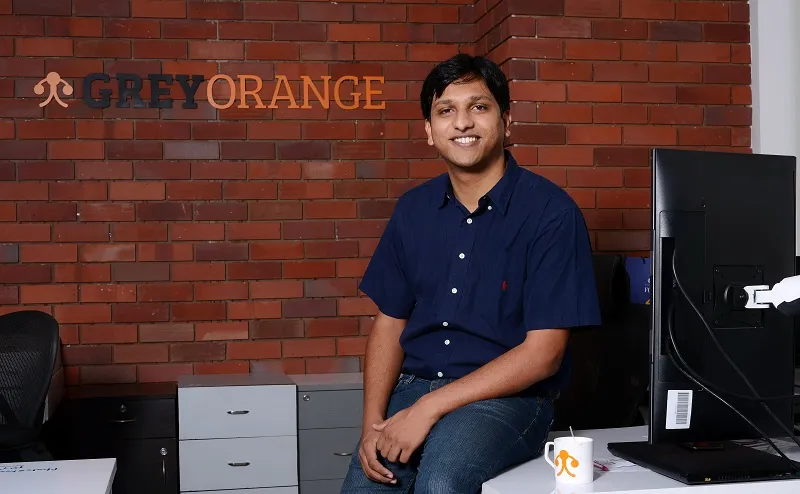
Team building, the GreyOrange way
In the early days of GreyOrange, Akash used to hire people who were ready to learn and had a good understanding of basic sciences-- physics and mathematics. Lately, he has changed his approach and now he looks for the following kinds of people:
- Those who understand a specific stream very well, like electronics, embedded, software or mechanical, and are curious about their environment.
- Those who have the will to grow into cross-functional roles. They might not have an in-depth understanding of a specific field, but understand the system overall.
- Those who have the design sense for hardware.
Also read - How a small-town commerce graduate became CTO of a multibillion-dollar company
The next big thing
Akash is a big fan of flexibility and believes that the way supply chain is growing, the only way to build an efficient supply chain is by making it extremely flexible. He says,
In next three to five years, we're looking at warehouses running with mobile platforms with changeable accessories. We really want to get to the point where you don't have any fixed infrastructure that's running in the warehouse. These mobile platforms can attach themselves with different accessories and can work as lifting units, or conveyers or robotic arms or static platform.
In order to get there, there're certain technology platforms that need to be built which will enable that. Akash and his team is already working on it at the moment (along with architecturing the entire solution). Once that’s done, it’ll take another year or two to integrate with the system. The team is also working towards introducing the concept of unibots (similar to human beings) in the next five to seven years.
Akash wants to run one of the largest warehouses with 10,000 robots very soon. He is also keen to build GreyOrange as a company where he would still want to work ten years hence. He’s making sure that the company retains the culture of innovation and building new products. He adds, “GreyOrange’s products are disruptive. For example, while other companies in the world offering linear sorters have a lead/installation time of at least three-four months, we do it in as less as four weeks.”
He wants to stick to producing simple elegant hardware with extremely complex software which disrupts the industry.
Sincerity – the utmost virtue
Akash believes in being sincere to oneself and one’s work. For the first three-four years of the company, he was always the first to reach office and last to leave. He felt it as a responsibility that till any employee was in the office, he should be there with him/her to support, to help. He says,
The biggest fear that you have as an entrepreneur is that if you fail, then you shouldn't have this in your heart that you didn't give your best.
You can connect with him on Linkedin or Twitter.